3Dプリンターが話題となって10年近くたち、現在はAmazonなどのECサイトでも、数万円で購入できるようになりました。多くのプロダクトは机の上に置ける、あるいは冷蔵庫ほどのサイズです。昔に住んでいた家、乗っていた車などミニチュアの記念品として残したいアイテムや、2Dキャラクターの造形化など、手のひらサイズのコンパクトな造形物の出力を得意としています。
そういったコンシューマー用途の3Dプリンターとは別に、業務用途の大型3Dプリンターも進化しています。2019年に創業したロボットベンチャー企業、Polyuseが開発した建設用3Dプリンターもその1つ。同社によれば、業者向けとしては日本初の建設用3Dプリンターとなるそうです。
海外では2010年代より、土木現場や建築現場で使われる大型3Dプリンターの開発が活発化していますが、モノづくりに長けているはずの日本ではなぜ話題となってこなかったのでしょうか。そして土木・建築向きの大型3Dプリンターは、日本におけるどのような課題を解決してくれる可能性を秘めているのでしょうか。Polyuseの岩本卓也CEOに話を伺いました。
※情報開示:PolyuseはCoral Capitalの出資先企業です
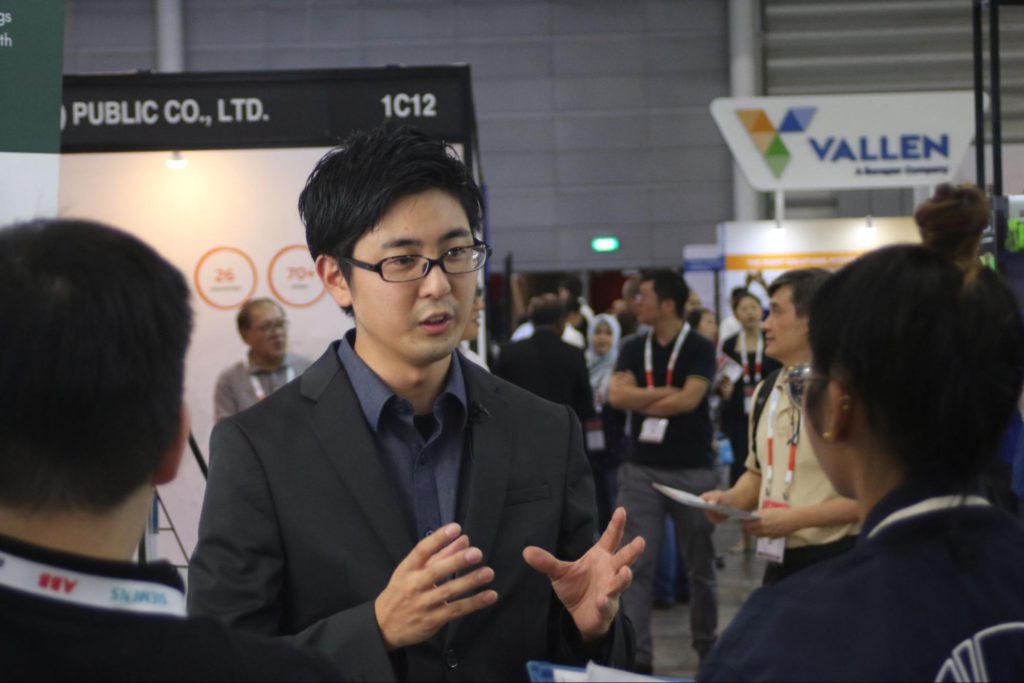
株式会社Polyuse代表取締役CEOの岩本卓也さん
日本ではじめて建築基準法をクリアした建築物をプリント
Polyuseの建設用3Dプリンターは、3DのCADデータにもとづき、セメント系の材料を積み重ねることで造形します。箱状のフレーム内を、出力ヘッドが自由に動き回る構造で、これは既存の3Dプリンターと同じです。しかしよく見ると、サイズが大きいということに気がつきます。なんと縦横高さが最大3メートルもあるのです。
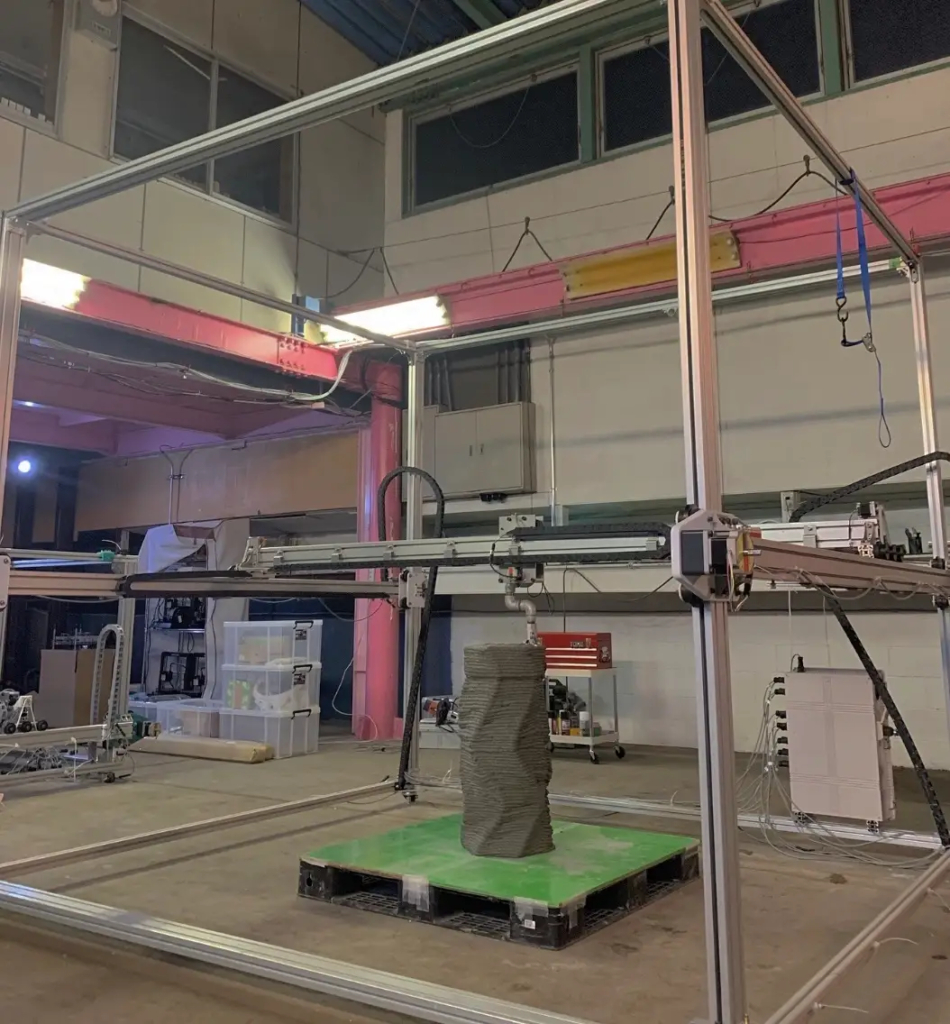
Polyuseの建設用3Dプリンター
人間よりも高いフレームゆえに、出力できるサイズも段違い。今回、建築物の施工に利用したような高さ1.5m、横幅4mのパーツがプリント可能です。
この建設用3Dプリンターで出力したパーツを組み合わせることで、建築物まで作ることもできます。しかも、日本国内の建築基準法をクリアする安全性の高い建築物を。
Polyuseは2022年2月、株式会社MAT一級建築士事務所が設計した建築物を建設用3Dプリンターを用いて出力し、群馬県渋川市に施工しました。
建築物の形状は建設用3Dプリンターが得意とするR形状を含む、12個の建築部材を組み立てて施工したもの。横幅は約6メートル、奥行きは約3〜4メートル、高さは約3メートルの平家建てとなります。これまで建築確認申請が不要だった10平方メートル以下の建築物ではなく、17平方メートル超の広さを実現しました。
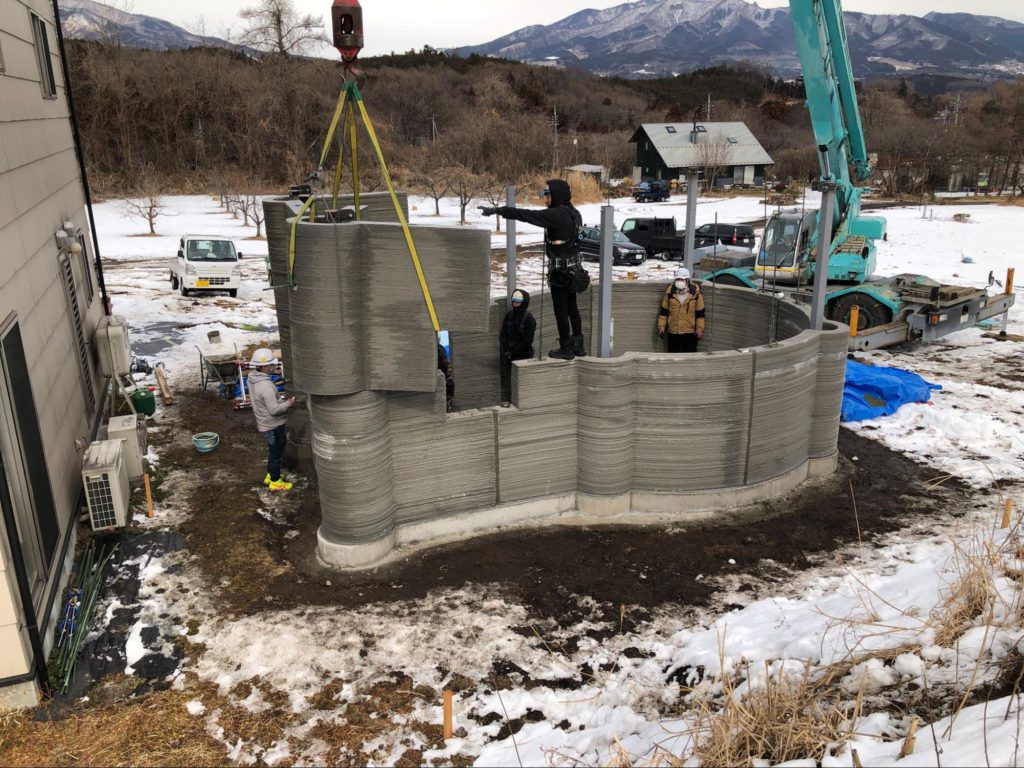
群馬県渋川市での施工風景
同社調べによれば、今回造形した建築物は、日本国内における初の3Dプリンタ施工による建築確認申請取得の建築物となります。構造計算を必要としない4号建築物という枠組みに収まる建築物ではありますが、これは快挙といえます。
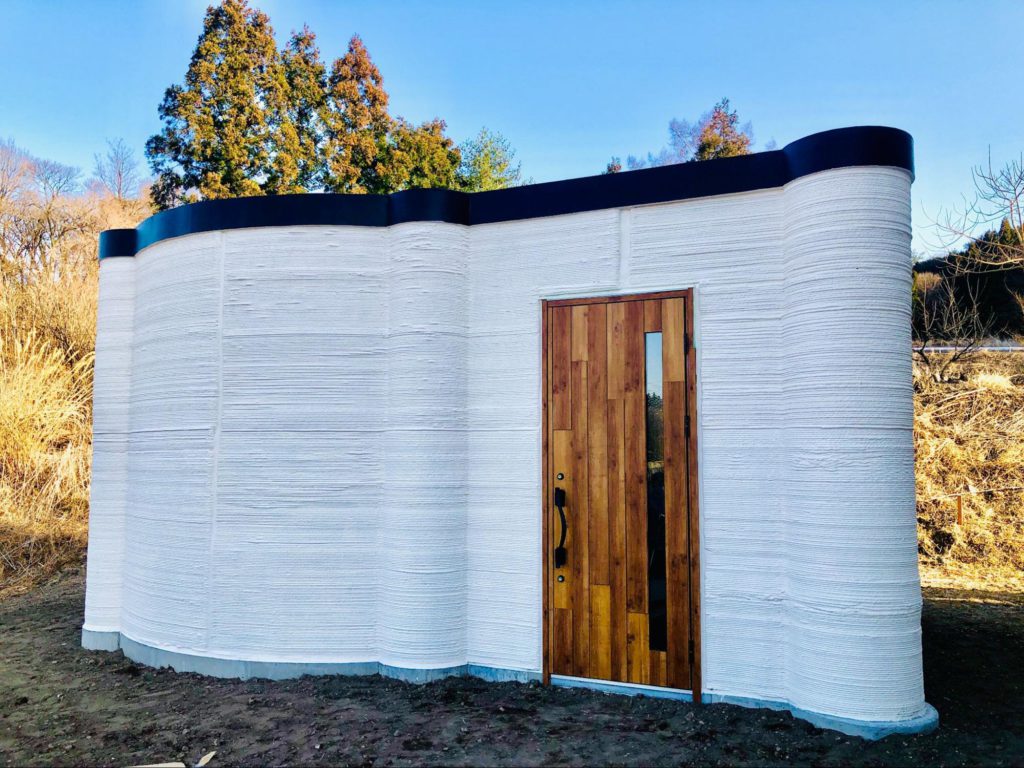
群馬県渋川市で3Dプリンタ施工を行った建築物
狙いは建設現場の人手不足の解消
Polyuseの狙いは決して住宅のような建築物だけではありません。建設用3Dプリンターを開発した背景には、日本の社会インフラが危機的状況にあることが大きく関わっています。
国土交通省のデータによれば、建設後50年を経過して寿命を迎える社会インフラの割合は、道路橋が約18%(2018年)→約43%(2023年)→約67%(2033年)、トンネルが約20%(2018年)→約34%(2023年)→約50%(2033年)、港湾岸壁が約8%(2018年)→約32%(2023年)→約58%(2033年)と、どれも半数以上が寿命となっています。
この由々しき事態に加えて、人手不足の問題も忍び寄ってきています。
日本型枠工事業協会によれば、現時点でコンクリートを使った躯体工事の就業者の4割が55歳以上。数年後には3分の1が減ることが予想されており、社会インフラ維持のための労働力需要は伸びていく反面、就業者が減るというギャップが目立っています。
建設用3Dプリンターがあれば、土木・建築現場での作業時間を大幅に短縮できます。
前述した建築物の場合、職人の工数は従来の工法では34人日必要でしたが、3Dプリンターの施工では15人日と半分以下の工数に収まりました。工事期間についても従来の工法は躯体工事に18日かかるというのが一般的でしたが、3Dプリンター施工では3日まで短縮することに成功しました。
「通常の鉄筋造に使うセメント系材料とは異なり、特殊資材を追加しているために材料費のコストは高くなります。現時点では工事期間を短縮できたとしても、トータルのコストは変わらないと思います。しかし現場における人手不足を解消するという面において、大きな役割を果たすと考えています」(岩本氏)
Polyuseの建設用3Dプリンターは、前述した老朽化の進む道路橋やトンネルなどの社会インフラの現場でも実証実験が進んでいます。
2021年6月には、前田建設工業との共同実証実験で円柱型の集水桝(水を溜め込む施設)を造形し、取り換え工事を実施しました。その後、実際の民間企業によって発注された土木工事、国土交通省管轄の土木工事においても活用されています。
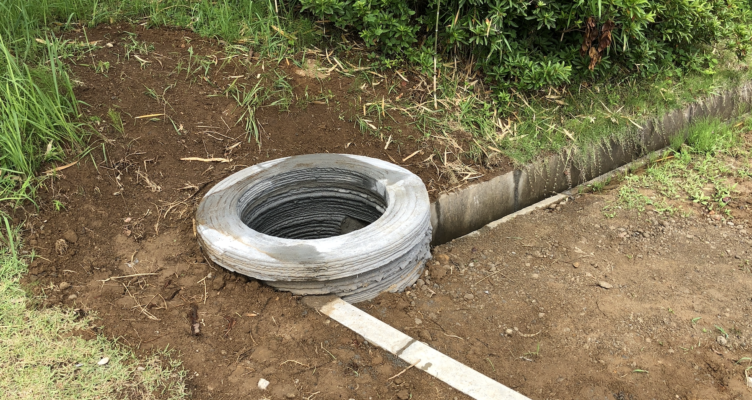
前田建設工業との共同実証実験で造形した円柱型集水桝
特に2022年1月に実施された土佐国道事務所(国土交通省四国地方整備局)の発注案件にて高知県の入交建設株式会社によって施工された集水桝の事例は、業界騒然となっているそうです。これまで公共機関の発注案件で建設用3Dプリンターによる構造物の使用実例がなく、国内初の取り組みとして評価されていて、日本の建設工事のうち約4割を占める公共土木工事に適応されることは建築確認申請取得した建築物と並ぶ快挙といえます。
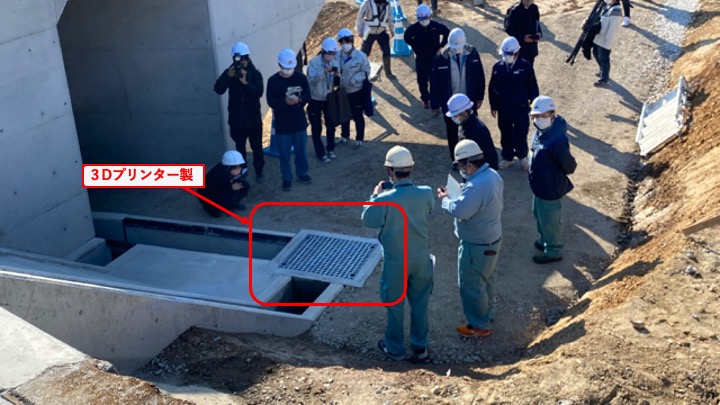
高知県にて公共工事で初めて本設構造物として利用された集水桝
「橋梁など大型の構造物に対しても、家屋のような建造物と比較的同じ手法で対応できます。また3Dプリンター施工の建築物では、出力した12個の部材を繋げて作りましたが、この『繋げる』という技術も確立できたので、大型の構造物でもいくつかの部材に切り分け出力しておいて、現場で繋げて施工するプロセスが取れると考えています。さらに、部分的に置き換えるところや欠落した部分を補修する箇所に関しても3Dスキャナーで形状を読み取り、その必要な部分だけをすぐに出力することもできます。これから活用の機会はますます増えてくると考えています。」(岩本氏)
日本の気候にマッチしたセメント系材料の研究開発
メリットが多いと実感できる建設用3Dプリンターを用いた3Dプリンター施工。なぜ日本では普及しなかったのでしょうか。そこには建築基準法という、日本ならではの厳しい安全基準の壁がありました。
海外では2010年代から建設用3Dプリンターの市場が活性化していきました。しかし海外の建設用3Dプリンターの多くは、「壁を作ることはできても内部は空洞であり、重量を支えるための部材を作る場合において法適応させることが現時点では難しい」と岩本氏は指摘します。こうした理由があったことから、日本での導入例は極めて少なかったとみられます。
「日本の建築基準法では安全性を確かめるために『構造計算』と呼ばれるプロセスがあります。しかし現時点では、外装だけを3Dプリントした場合に安全性をクリアできるかどうかを判断できないんです。その研究結果は現在検証中であり、計算方式も確立されていません。そこで我々は各パーツの内部にもモルタル素材を充填して1つの部材とする等の技術によって、従来のコンクリート壁に適用される基準と同等の安全性を出すことに成功しました」(岩本氏)
3Dプリンターで建築基準法の安全基準をクリアするにあたっては、Polyuseでも開発が難航したそうです。
「壁の内部をコンクリートで充填するためには、それだけ長時間出力し続けないとなりません。また出力しているセメント系材料の詰まりや、出力中の壁が重さで曲がるといったトラブルもありました。日本は高温多湿かつ雨が降りやすい環境であるため、海外と比べると屋外でのコンクリート・モルタル施工が不利な面もありました」(岩本氏)
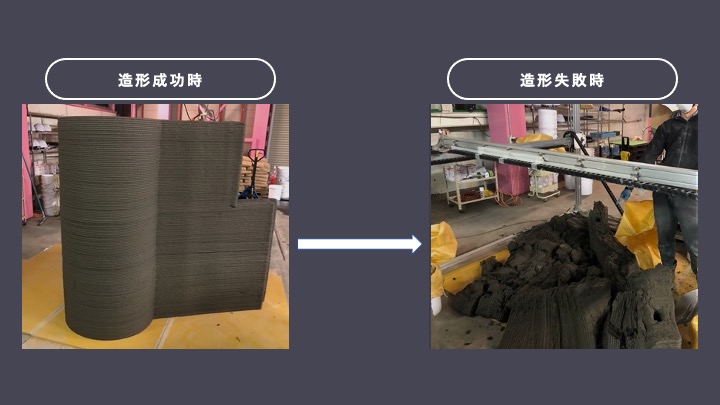
群馬県渋川市に施工した建築物の部材。条件が少し変わるだけで、右の写真のように造形に失敗してしまったそうです
「開発は難航しましたが、早い段階でトライ&エラーができたことで、3Dプリンター施工に適したセメント系材料の研究開発も進みました。また、天候や気温に左右されないようにするために、必要な部材は工場内で造形し、トラックで搬入するという手法にも繋がりました。結果として現時点においては、海外メーカー製の建設用3Dプリンターは連続稼働時間が1~2時間くらいですが、弊社の建設用3Dプリンターは6~7時間の連続稼働が可能となりました」(岩本氏)
3Dデータを共有すれば、どの地域に設置した建設用3Dプリンターでも同じ部材が作れます。これは災害時の仮設住宅需要においても効率的。部材を組み合わせて建築物を作る施工法ゆえ、長く住むうちに家族構成が変化した際も家全体の平米数を変えることが可能です。3Dプリンター施工の住宅はプレハブ住宅より断熱性が高く、熱い・寒い地域でも居住性に優れている点もメリットとして挙げられます。
施工期間の時短につながり、現場における人材不足の問題をカバーする。3Dデータに合わせた出力ができるからこそ、自由なデザインが可能。仮設住宅としても居住性に優れているなど、建設用3Dプリンターを用いるメリットはたくさんあります。さらに今後は、どのようなメリットに繋がっていくのでしょうか。
「今回の建築物施工では、弊社の建設用3Dプリンターが土木も建築もいけるということを証明できました。今後はより多くの建設現場で活用していただけるように工夫を重ねて、未来のインフラ作りを支援していきたいです。将来的にはスマートシティなどのハイテク環境の礎を支えることも考えています」(岩本氏)